Le nombre déjà important d'objets connectés (aujourd'hui 10 milliards d’objets circulent dans l'internet des objets) est en croissance constante (plus de 30 milliards en 2020, pronostique ABI Research). Un tel développement n'est possible qu'en ayant recours à des techniques de fabrication rapide et à très bas coût. Ceci concerne en grande partie des objets réalisées en technologie « micro-électronique souple », pour lesquels des pistes métalliques (antenne notamment) doivent être réalisées. Dans cet objectif, le Laboratoire de Chimie des Surfaces et Interfaces (LCSI) de l'IRAMIS a mis au point un procédé très innovant de métallisation des polymères par impression jet d’encre.
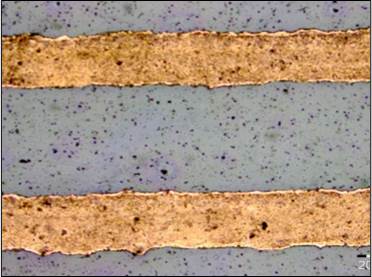
L'étiquette attachée aux objets est l'élément indispensable pour construire un système de données permettant leur identification ou leur suivi. Au-delà de l'étiquette passive (telle que la simple lecture d'un code barre au supermarché), les dispositifs de la micro-électronique permettent de créer des étiquettes contenant beaucoup d'informations et capables d'être modifiées à volonté. De telles étiquettes sont en général constituées d’une puce électronique sur substrat polymère (électronique souple), raccordée pour les besoins de la communication à une antenne métallique. Ces objets communiquent ainsi sans fil (Wireless Fidelity) par différents moyens (puce RFID : Radiofrequency Identification, et NFC : Near Field Communication) selon divers protocoles (échange radio courte distance Bluetooth par exemple). Nos cartes de transport et certaines cartes de paiement communiquent ainsi par RFID.
Les technologies de l’électronique souple tentent de s’affranchir des technologies lourdes associées aux salles blanches de la microélectronique silicium. Les procédés en bande continue (Roll-to-Roll) sont incontournables pour répondre aux cadences de productions exigées, mais sont difficilement compatibles avec les procédés de photolithogravure. Il s’agit là de procédés soustractifs issus des filières technologiques descendantes « top-down » qui procèdent par élimination de matière (lift-off). Par opposition, les procédés d'impression, tels que les procédés par jet d'encre, sont additifs et s’inscrivent dans une construction « bottom-up », répondant beaucoup mieux aux contraintes économiques et environnementales actuelles : la génération de déchets liquides et de COV (Composés Organiques Volatils) est par exemple très faible. Ces techniques prennent une place de plus en plus importante sur ce marché en forte croissance.
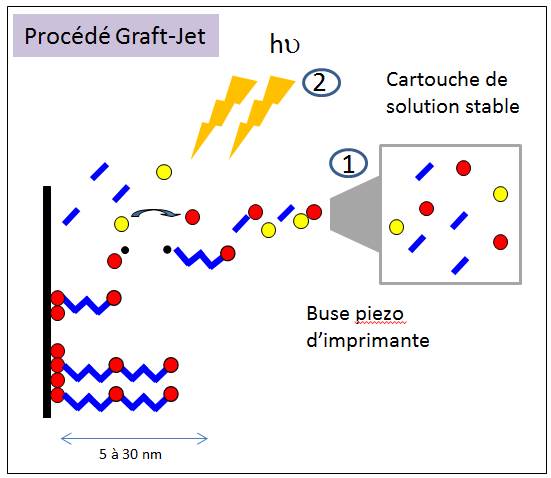
Les procédés de fabrication par impression jet d’encre des pistes métalliques sur plastique utilisent aujourd’hui des encres conductrices formées de nanoparticules d’argent. On retrouve ce procédé par exemple dans la fabrication des antennes RFID, d’interconnexions pour le photovoltaïque et aussi d’OLEDs. Deux contraintes fortes subsistent aujourd'hui dans ce type de procédé :
1/ Pour obtenir les valeurs requises de conductivité, il faut interconnecter les nanoparticules métalliques et éliminer les composés organiques qui stabilisent les solutions. Un traitement thermique au-delà de 150°C est le plus souvent nécessaire, ce qui limite considérablement le type de matériaux plastiques compatibles (et élimine notamment les moins chers) et augmente le coût de production.
2/ l’adhésion de la piste métallique sur le polymère n’est pas de grande qualité si rien de particulier n’est fait : la simple projection d’une encre ne crée pas de greffage chimique indispensable à la bonne tenue et donc à la fiabilité du composant réalisé.
Un procédé innovant développé au Laboratoire de Chimie des Surfaces et Interfaces (LCSI) de l'IRAMIS remédie à ces deux problèmes. Pour bien présenter la rupture technologique et les bénéfices du procédé revenons à ses origines : en 2007 le laboratoire a mis au point un procédé chimique capable de produire un primaire d’adhésion sur plastique permettant une métallisation ultérieure sans étape électrochimique (Electroless). La start-up Pégas-Tech est aujourd’hui sur ce secteur et exploite ce procédé de polymérisation sur surface Graftfast©, en partenariat avec des industriels de l’automobile (plastique métallisé d’éléments décoratifs intérieurs et extérieurs).
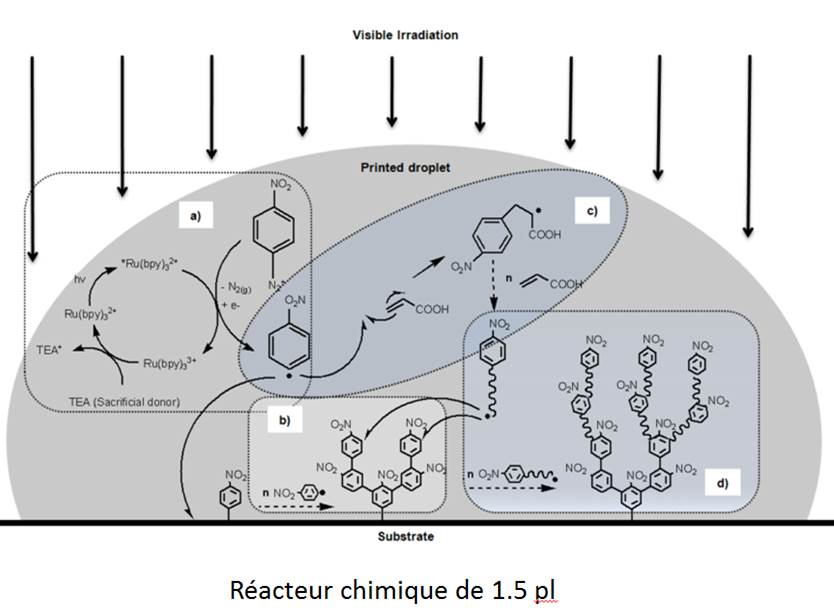
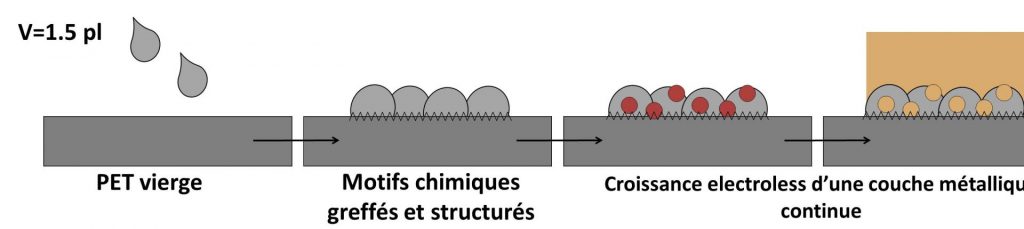
Ce procédé a été initialement mis au point pour le traitement de pleine surface. L'innovation porte aujourd'hui sur son adaptation à l'impression jet d’encre. La simple transposition des solutions réactives du procédé original Graftfast© dans des cartouches jet d’encre s’est avérée impossible du fait d’un bouchage rapide des buses de faibles diamètres (20-30 µm) par le phénomène rapide de polymérisation. Il était donc nécessaire d'utiliser une encre « inerte » et de séparer en deux étapes l'application des solutions réactives sur les surfaces et leur activation chimique. Le déclencheur de la réactivité est un agent photosensible (ici un réducteur photochimique) qui est activé par le simple éclairage d'une lampe à incandescence de 100 W.
L'activation par la lumière s'est révélée être un point clé du procédé. La formulation très particulière de l'encre conduit à une chimie radicalaire très sensible à l’oxygène au sein du microréacteur, que représente une petite goutte de jet d’encre de 1.5 pl (10-12 litre). Pour ce procédé, mis en œuvre à l'atmosphère ambiante, la gouttelette est initialement saturée d’oxygène (5 10-4M à 20°C) et il a cependant été possible de permettre aux réactions attendues de s’y dérouler : l’astuce consiste à créer une déplétion temporaire de l’oxygène par une consommation sacrificielle des premières espèces radicalaires formées. Par l'activation quasi-instantanée par la lumière de l'ensemble du réactif, la réaction rapide se poursuit alors sans oxygène, avant que l’oxygène de l'air ambiant revienne se dissoudre à nouveau dans la gouttelette.
A l’issu de l’insolation, le procédé se traduit par la création d’une image latente chimique (greffée sur la surface plastique) qui va accueillir la croissance « electroless » du métal. Le procédé résout ainsi à la fois le problème de l’adhésion sur plastique, par la création d’un lien chimique interfacial, et celui de la conductivité en faisant croitre directement un véritable film métallique continu sur cette image. Le procédé présente l'avantage décisif d'une croissance métallique réalisée à basse température (45°c) et active dès 25°c. Enfin, l'impression jet d’encre présente l'autre avantage de permettre la fabrication de petites séries, voire de pièces uniques et sur-mesure, très demandées en développement microélectronique. Des contacts industriels sont d'ores et déjà pris sur cette technologie innovante et les brevets associés prêts à être licenciés.
Ce travail a été l'objet du travail de thèse d’Alexandre Garcia: « Métallisation anélectrolytique des polymères induite par des ligands« , pour lequel lui a été décerné le « Prix de thèse, catégorie recherche finalisée » du Centre de compétences NanoSciences Ile-de-France (C'Nano-IdF).
A. Garcia travaille aujourd'hui dans les laboratoires de Saint Gobain Recherche.
Contacts CEA : Pascal Viel et Thomas Berthelot (IRAMIS / SPCSI / LCSI).
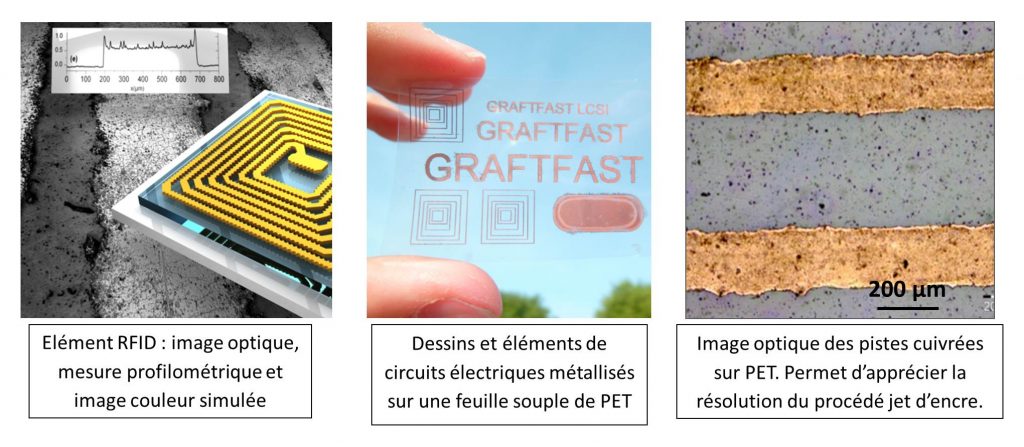