Flame spray pyrolysis for the synthesis of nanomaterials
The Flame Spray Pyrolysis process (FSP) developed at LEEL is a continuous flow gas phase synthesis method used for the elaboration of nanoparticles under the form of dry nanopowders. This process is based on the flash-evaporation of a solution made of precursors dissolved in a combustible solvent, sprayed as a droplets aerosol into a combustion flame (pilot flame). In the gas-to-particle reaction path, burning of the solution vapour leads to the formation of a high temperature reaction medium (synthesis flame), where the homogeneous nucleation of the primary particles is achieved by the cooling of the gas phase when leaving the burner vicinity. During their transport to the filter as a dry aerosol, primary particles (<10 to ~ 100 nm in size depending on the conditions) collide and form small hard aggregates and large soft agglomerates finally collected as dry nanopowders.
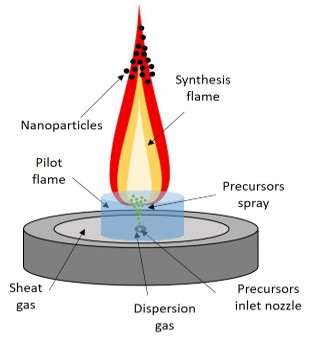
The solution based approach combined to the very fast reaction time (~ 1 ms) and high temperature (1500 – 2000°C) of this out-of-equilibrium process ensures the homogeneity and crystallinity of the obtained nanoparticles without any calcination or crystallization post-treatment. Simple lab-scale installation such as LEEL’s one enables the continuous production of several g/h for multi-elements nanopowders, and up-scaling is achievable as FSP and its derivative are already well known in the industry and employed for the very large scale production of fumed silica, TiO2 (Evonik P25), or graphitic carbon black.
Originally dedicated to simple binary oxides spherical nanoparticles, FSP was reported for the synthesis of more than 500 different oxide materials with applications in various fields such as energy storage (batteries), fuel cells, (photo,electro) catalysis, or magnetic applications. More recently, FSP was developed towards the elaboration of more complex compositions (multi-element phases such as Nasicon, doped or substituted structures) and morphologies (core-shell, coatings, composites…). Large (100 nm – 1 µm) spherical, dense or hollow, particles can also be prepared by favouring the droplet-to-particle reaction path (Flame-Assisted Spray Pyrolysis, FASP). Non-oxide materials (metallic alloys, carbides…) were even obtained for some metals despite the presence of oxygen in the pilot flame.
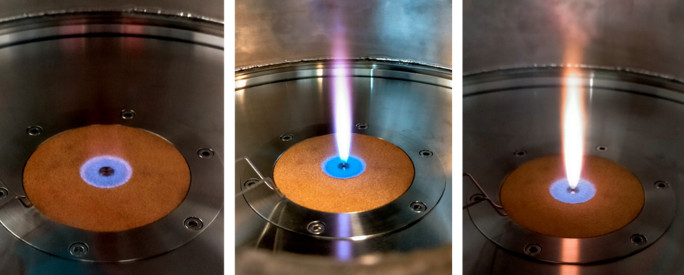
In LEEL, FSP is specifically employed to provide the lab with innovative nanomaterials for its own different research topics, such as electrode materials or solid electrolytes for post-Li batteries applications. FSP is also recently involved in more specific studies for electrolysers (H2 production) in collaboration with SPMS lab (Centrale-Supelec) and for magnetic applications in collaboration with DES/Liten and DRF/SPEC laboratories. A better understanding of the FSP process, and in particular of the nanoparticles formation mechanisms in flames, is also at stake in the context of a collaboration with EM2C lab of Centrale-Supelec. This lab benefits indeed of a deep expertise in combustion simulation and especially in the formation of solid particles in turbulent flames.
FSP process by itself is also under strong research efforts in LEEL in the frame of Diadem PEPR initiative (https://www.pepr-diadem.fr/en/). As one of the FastNano targeted project platforms, LEEL’s FSP setup will be upgraded with in situ LIBS spectrometry developed with LEDNA lab by the end of 2024. This device, assisted by AI to provide information in real time, will give the particles chemical composition as they grow, enabling the direct study of the effects of FSP parameters on materials stoichiometry and thus avoiding time-consuming trials with post synthesis characterization. In the frame of FastNano, LEEL’s FSP setup will also be coupled to LEDNA’s co-deposition reactor in order to elaborate nanocomposite layers or coatings with an independent choice in the nature of the nano-inclusions (directly extracted from FSP reactor to the co-deposition chamber) and of the matrix (grown simultaneously in the co-deposition chamber by PVD). Composition of the growing composite layer will also be investigated by in situ and real-time LIBS, enabling direct feedback on both co-deposition and FSP synthesis parameters. The two LIBS systems will communicate their results to an AI supervision software able to adjust all parameters to obtain the targeted layer composition. LEEL’s FSP setup, as well as LEDNA’s co-deposition tool, are part of the platforms shared with the European scientific community in the frame of the Research Infrastructures project RisEnergy (https://eera-energystorage.eu/risenergy-proposal.html) aiming at accelerating the emergence of innovative materials solutions for renewable energy. In the frame of this project, foreign researchers from the EU can obtain funding to visit and use the shared platforms for renewable energy related research projects.