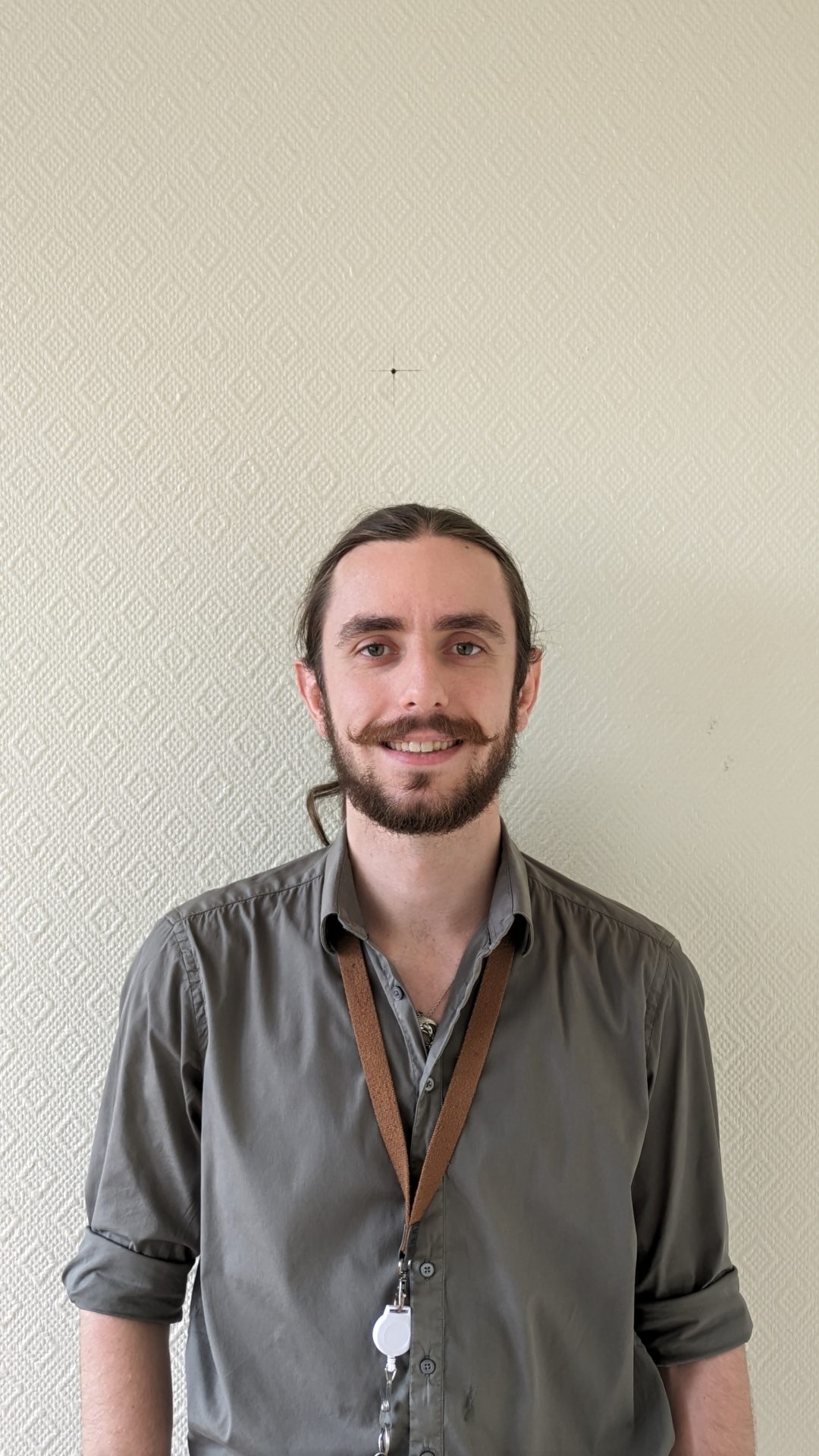
PhD Student
Tél. : +33 1 69 08 47 84
E-mail :
PhD Topic : Development and study of laminated composite material integrating carbon nanotubes for launcher cryogenic tank application
The emergence of new “low-cost” launcher technologies motivates the research and development of new material architectures that are both lightweight and resistant to thermomechanical and chemical stress. In particular, the development of new composite structures can play a very important role in terms of mass savings. Among the various areas already initiated, reducing the weight of the cryogenic tank can significantly improve the performance of a propulsion stage.
In this area, studies report the development of composite materials with varied organic matrices (thermosetting or thermoplastic) integrating reinforcements of different types: glass fibers, Kevlar fibers or carbon fibers, carbon blacks, graphene, silica nanoparticles , and even more recently carbon nanotubes (CNTs). The latter, due to their exceptional physical and mechanical properties as well as their lightness, could bring notable advantages to composite materials potentially usable for the creation of cryogenic tanks. However, the state of the art reveals a lack of study of these nanomaterials in cryogenic environments. Indeed, to our knowledge, composite materials incorporating CNTs have been studied in a liquid nitrogen environment, thus making it possible to qualify their behavior at low temperatures in terms of damage, but no study deals with the compatibility of these materials in environments of interest such as liquid oxygen.
In this context, a preliminary study carried out between the CEA and the CNES made it possible to develop the first innovative composite elementary bricks integrating CNTs. This led to the selection of the cyanate ester matrix (called CE) and to initial tests under a pure gaseous oxygen atmosphere (Gox), making it possible to determine the self-ignition temperature of the material. The results of these trials demonstrate a beneficial effect of CNTs [1].
The subject of this thesis is part of a thesis project whose objective is to find the best way to integrate carbon nanotubes into laminated composite materials, capable of bridging the microcracks of the matrix of these composites, in order to limit fuel leaks from cryogenic launcher tanks. Knowing the mechanical and thermal stresses, the aim will be to demonstrate the effectiveness of CNTs with respect to the tolerance to damage of the material. Damage tolerance is directly related to strength and waterproof performance.
To do this, three ways of integrating carbon nanotubes are envisaged: 1-Growth of carbon nanotubes (CNTs) directly on carbon fibers by CCVD [2], 2-Transfer of a mat of carbon nanotubes aligned on CE pre-impregnated carbon fiber fabric, and 3-Random dispersion of carbon nanotubes in the matrix. The approach will consist of adjusting the synthesis parameters (duration, injection, reactive atmosphere, etc.[3]) with the aim of controlling the characteristics of the CNTs formed (alignment, length, etc.). Particular attention will be paid in particular to the control of the length, diameter and density, in particular by electron microscopy analysis (SEM and TEM) as well as the structural quality of the CNTs by Raman spectrometry.
[1] J Bouillonnec, D Champonnois, K Mathis, M Pinault, M Mayne-L’Hermite, et D Miot. EUCASS proceeding 2022, 14 [2] M Delmas, M Pinault, S Patel, D Porterat, C Reynaud, M Mayne-L’Hermite. Nanotechnology 2012, 23 [3] C Castro, M Pinault, D Porterat, C Reynaud, M Mayne-L’Hermite. Carbon 2013, 61