ALICE is an original and safe-by-design method for the elaboration of nanostructured coatings composed of nanoparticles embedded in a matrix.
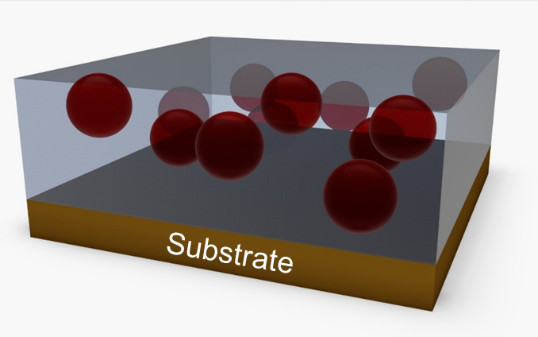
This versatile single step process operates under vacuum by combining jets of nanoparticles with magnetron sputtering. The chemical nature of nanoparticles and matrix can be chosen independently. Moreover, any source of nanoparticles in the gas phase can be used. For example, nanoparticles can be synthesized in-situ by laser driven pyrolysis or combustion processes. A classical aerosol generator from previously synthesized nanoparticles can also be used.
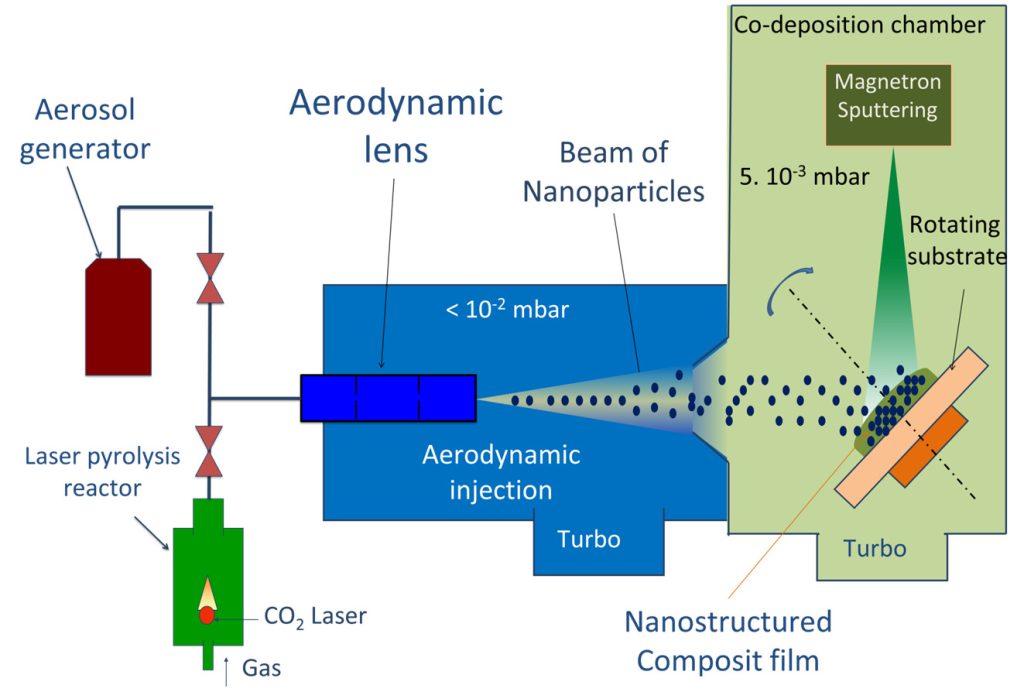
In the following figure, an example of the results of numerical calculations carried out using the Flow EFD software (Mentor Graphics) in two configurations is given. In a) are represented trajectories of nanoparticles (red) under conditions of collimated jet with 15 nm gold nanoparticles. In b) are shown trajectories of nanoparticles under divergent jet conditions with the same nanoparticles. The corresponding deposits made experimentally with similar nanoparticles on a paper substrate placed at 260 mm from the outlet of the aerodynamic lens are also presented in each case. With a diameter of the acceleration nozzle of 4 mm, the observed deposit is very sharp, only few tenths of millimeter in diameter. With a smaller diameter of 2.2 mm, a larger diameter of more than 30 mm can be covered with nanoparticles in a homogeneous deposit.
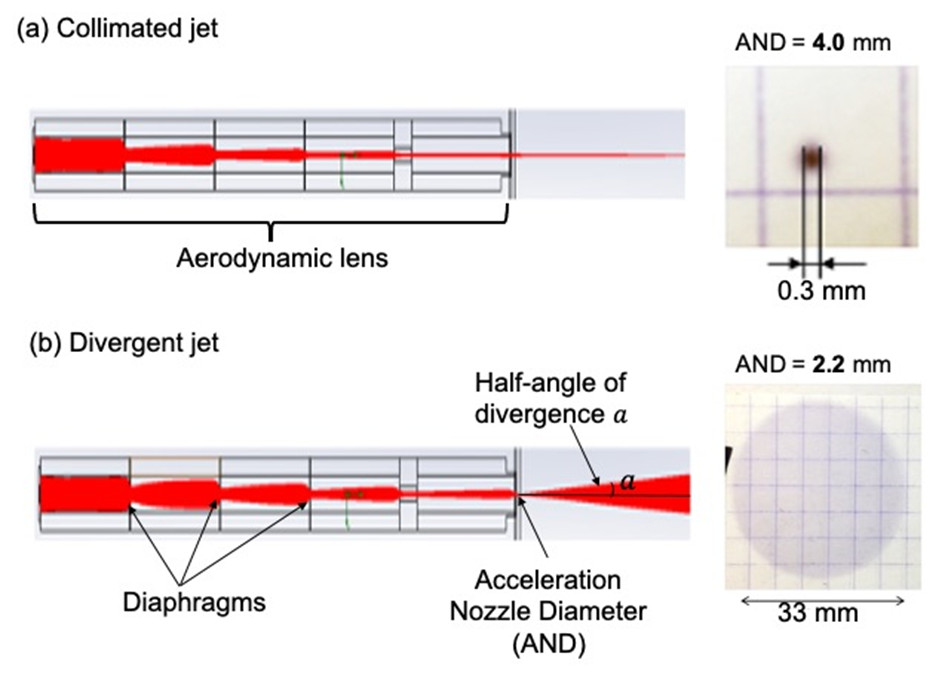
The ability to elaborate large and homogenous nanostructured films were investigated with different types of nanoaerosols of different sizes and densities. Samples composed of metallic nanoparticles in a ceramic matrix and the opposite are shown in the following figure. Due to the simultaneous deposition of nanoparticles and matrix, the morphology of the thin films and consequently their porosity and roughness are closely related to the density of nanoparticles embedded in the matrix.
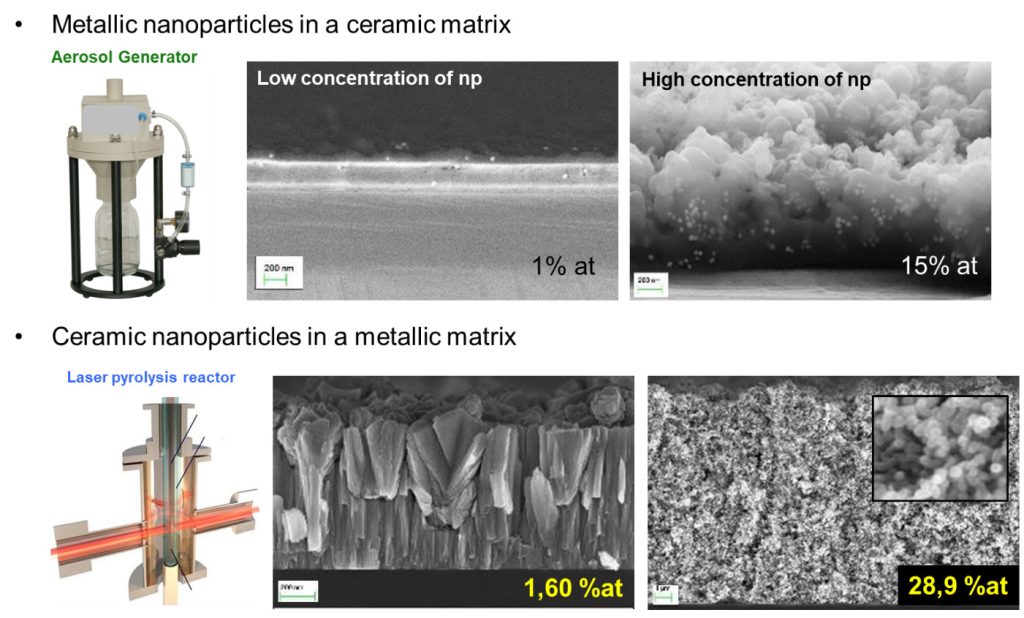
In view of industrial use, the addition of multi-aerodynamic lens system combined with smart masking of the corresponding jets and the optimization of the sputtering process configuration can lead to the growth of a homogeneous nanocomposite thin film on a large surface (tens cm2). The use of several aerodynamic lenses in parallel makes it possible to ensure good coverage of a larger surface area substrate by the overall flow of nanoparticles. Each aerodynamic lens produces a jet of nanoparticles with the same divergence half-angle. The diameter of the acceleration nozzle as well as its distance from the deposition chamber is adjustable according to the half-angle of divergence of the jets, depending on the nature and size of the nanoparticles. Two or even more sputtering cathodes adjustable in distance and orientation are used, and the substrate holder and sputtering sources can move laterally. Furthermore, the use of two cathodes allows to alternate or simultaneously deposit several materials extending the possibility of the matrix choices (e.g., alloys, multilayer, etc.).
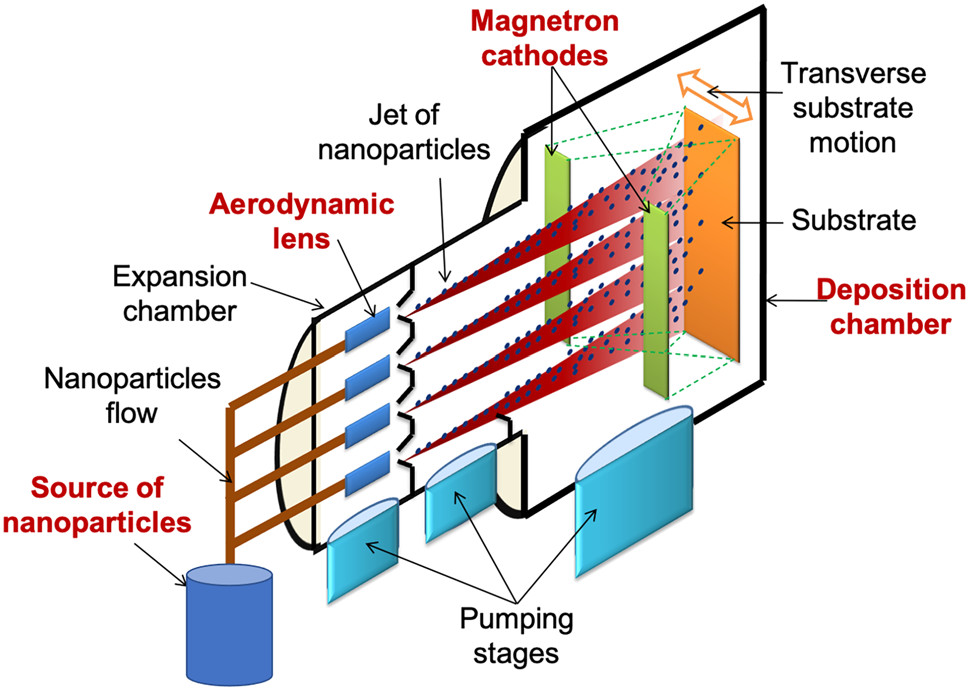